Technics: MIM
Quoted Condition: 2D / 3D Drawing / Sample
Package: Carton, Plastic Bag, Export Package
OEM/ODM: Welcome
Precision Processing: Mixing, Injection, De-Binding, Sintering
Production Time: 15-30 Days
Weight: 0.8g
Size: 15*9mm
Trademark: drome
Transport Package: Carton
Specification: 290*190
Origin: Suzhou, China
MIM(Metal powder Injection Molding) is the 5th generation of metal forming technology. Over 40 years of development, people gradually find more applications for MIM process especially in the 3C products application. From initial groping to mature stage, MIM technology witness the ups and downs of 3C products in the past ten years.
Fortunately, there are several parts of design such as hinges, fiber optic connector bases, and new style connectors are closely dependent on MIM technology. These products are being produced in a large number and MIM technology is being adopted by more and more.
MIM and CIM--Drome can provide one-stop service solution.
The basic attributes include:
1.Economical production of complex parts with weight from 0.03 to 200g from high-performance engineering materials.
2.Parts with high dimensional precision (±0.1%~±0.5%) and good surface quality (surface roughness 1~2μm).
3.Parts with high relative density (96%~100%), homogeneous microstructure and superior performance.
4.Adaptable to powders of various materials and wide application of the parts.
5.Material saving through the recycle of wastes, production process with high level of automation and suitable for mass production
Flow chart of metal injection molding
Application of MIM
Products Range:Â
Material |
 |
Typical Values |
 |
 |
Designation Code |
Density g/cm3 |
Tensile Properties |
Young's modulus, Gpa |
Un-notched Charpy Impact Energy,J |
Hardness,Rockwell |
 |
 |
UTS. Mpa |
Y.S. (0.2%), Mpa |
Elongation (in 25.4mm) % |
 |
 |
Macro (apparent) |
 Micro (converted) |
MIM-Fe2Ni |
7.8 |
280 |
115 |
25 |
 |
 |
55 HRB |
50HRCÂ Â Â Â |
MIM-Fe8Ni |
7.8 |
450 |
 |
12 |
 |
 |
84HRB |
50HRCÂ Â Â Â |
MIM-2200 (as sintered) |
7.8 |
290 |
125 |
40.0 |
190 |
135 |
45 HRB |
 |
MIM-2700 (as sintered) |
7.8 |
415 |
255 |
26.0 |
190 |
175 |
69 HRB |
 |
MIM-4605 (as sintered) |
7.8 |
440 |
205 |
15.0 |
200 |
70 |
62 HRB |
 |
MIM-4605 (Q&T) |
7.8 |
1655 |
1480 |
2.0 |
205 |
55 |
48 HRC |
55 HRC |
MIM-304L
|
7.8 |
500 |
 |
70 |
 |
 |
60 HRB |
 |
MIM-316L (as sintered) |
7.85 |
520 |
175 |
50.0 |
190 |
190 |
67 HRB |
 |
MIM-410
|
7.7 |
900 |
 |
7 |
 |
 |
 |
40 HRC |
MIM-420 (heat treated) |
7.7 |
1380 |
1200 |
12 |
190 |
40 |
 |
45-60HRC |
MIM-430L (as sintered) |
7.8 |
410 |
240 |
25.0 |
210 |
150 |
65 HRB |
 |
MIM-440C
|
7.8 |
700 |
590 |
15 |
 |
 |
 |
45-60HRC |
MIM-17-4PH (as sintered) |
7.8 |
900 |
730 |
6.0 |
190 |
140 |
27 HRC |
 |
MIM-17-4PH (heat treated) |
7.8 |
1190 |
1090 |
6.0 |
190 |
140 |
33 HRC |
40 HRC |
Â
Material |
Density( g/m 3)
|
Tensile Strength( Mpa)
|
elastic modulus( Gpa)
|
(thermal conductivity) W/(mk) |
( Thermal Expansion) 10-6/k
|
Copper(Cu) |
8.9 |
100 |
130 |
250 |
13 |
Invar(fe-36ni) |
8 |
300 |
205 |
20 |
5 |
Kovar Or F15 (Fe-29ni-17co) |
8.0 |
480 |
200 |
17 |
4.9 |
 Molybdenum-copper (Mo-15cu)
|
10 |
210 |
280 |
170 |
7 |
 Molybdenum-copper (Mo-20cu)
|
9.9 |
200 |
280 |
145 |
6.5 |
 Tungsten-copper (W-10cu)
|
17 |
500 |
340 |
209 |
6 |
 Tungsten-copper (W-20cu)
|
16 |
560 |
290 |
247 |
7 |
 Tungsten-copper (W-30cu)
|
14 |
420 |
260 |
260 |
11 |
product fieldÂ
Aerospace |
Airfoil Hinge,Rocket Nozzle,Guided Missile Spoiler,Turbine Blade Core |
Auto Industry |
Ignittion Control Lock Parts,Turbo Charger Rotor,Valve Guide Rail,Break Gear Parts and Sun Block Shack Parts |
Electronics |
Disc drive parts,Cable Connector,Electronic Valve Shell,Computer Print Head,Electronic Packaging Parts and Heat Sink Material |
War Industry |
Mine Rotor,Gun Trigger,Armor Piercer,Sight Base,Flechette Arrow and Shrapnel |
Medical Industry |
Orthopaedic Bracket,Internal Sewing Needle,Biopsy Forceps,Radiation-proof Cover |
Daily Necessities |
Watch Shell,Watch Belt,Watch Buckle,Golf head and Ball Seat,Sport Shoe-buckle,PE Mechanical Parts,Hole Puncher,Fish Catch and Bias Hammer |
Mechanical Industry |
Irregular Milling Cutter,Cutting Tools,Micro Gears and Sewing Machine Parts |
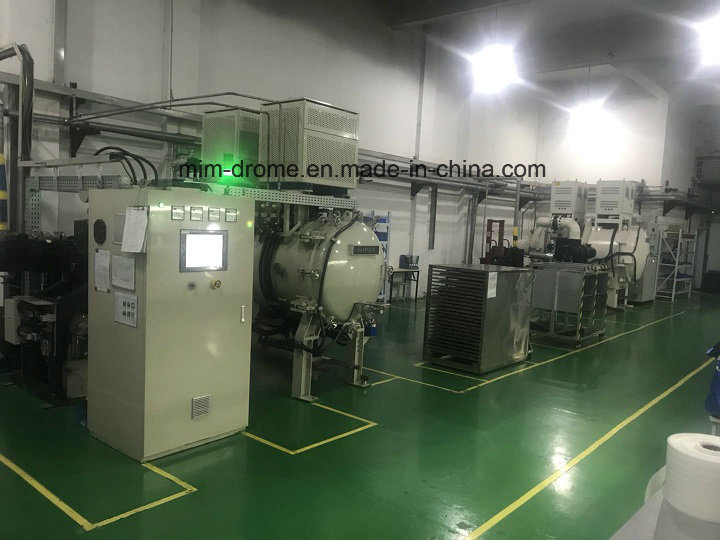
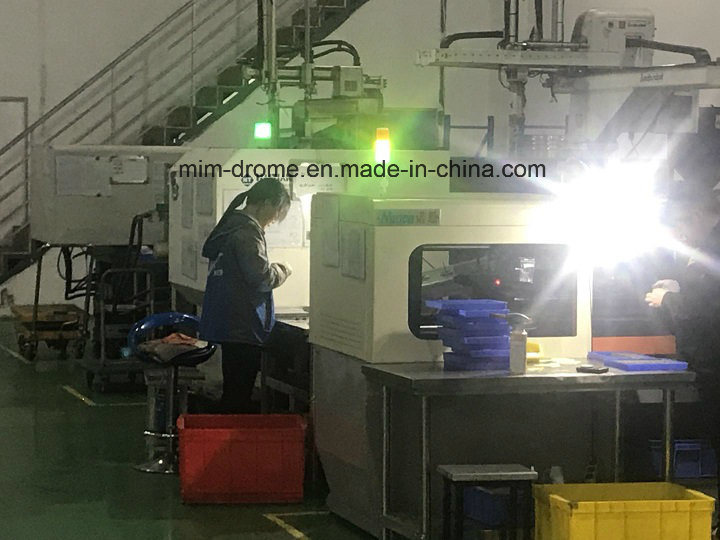
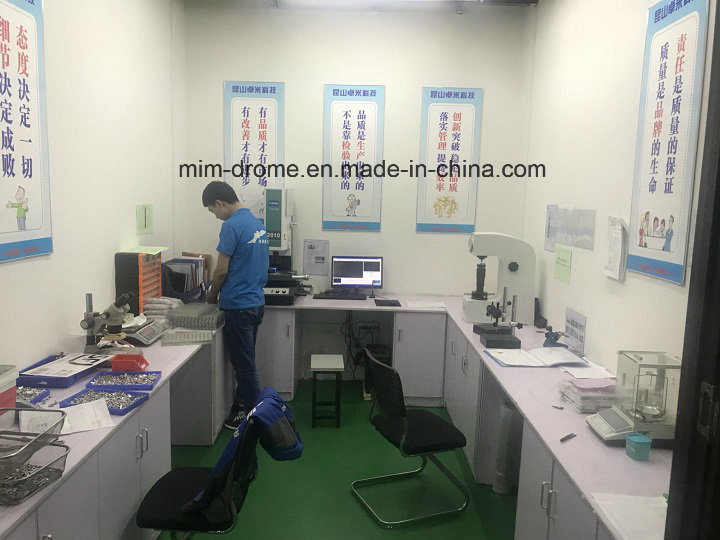
FAQ
1.How can I give you an offer?
Please send us product 2D/3Ddrawings.
PROCESS
Customer Inquiry →Engineering Communication →Cost Analysis →Sales Analysis →Quote to Customer
» 1 Work Days Only
» Submit RFQ with complete commercial terms
  Â
2. How to transport?
For small quantity, we choose TNT, FEDEX, UPS etc
For big quantity, air or sea would be available .
Â
3. packing details?
We attached our normal packing details Plastic disc/carton.
If the customer has specified packing specification, we will pack according to the customer's requirement.
Company Profile
- Design and manufacture Metal Injection Molding Parts, Ceramic Injection Molding Parts, Plastic Injection Molding Parts
- Current 10,000 Manufacturing Space, 30,000 in Construction;
- More than 200Â Employees, 17 Engineers;
- 2017 Sales Revenue >10 Million USD;
- IATF 16949, ISO 9001, OHSAS 18001, ISO 14001;
- 5% Revenue Yearly Invested in R&D;
- Best Machines, Germany Arburg, Japan Nissei, Japan Shimadzu;etc.;
- Serving Top Players in Industries of Auto, Consumer Electronics, Medical Appliance, etc. ;
Â
Blended Powder
A blended powder of tungsten carbide and Metal Alloy Powder can be used for laser cladding, a process used to deposit a layer of material onto a substrate using a laser beam. This blended powder is typically used as a feedstock material for laser cladding applications where high wear resistance and hardness are required.
Tungsten carbide is a hard and wear-resistant material that is commonly used in cutting tools, mining equipment, and other high-wear applications. It has excellent thermal conductivity and high melting point, making it suitable for laser cladding processes.
Metal alloy powders, on the other hand, are often added to the Tungsten Carbide Powder to enhance certain properties or tailor the characteristics of the final cladding layer. These metal alloys can include nickel, cobalt, chromium, or other elements, depending on the specific requirements of the application.
The blended powder is typically prepared by mixing the tungsten carbide and metal alloy powders in the desired ratio. This mixture is then fed into a laser cladding system, where it is melted using a high-power laser beam. The molten powder is rapidly solidified onto the substrate, forming a dense and wear-resistant cladding layer.
The resulting cladding layer can have excellent hardness, wear resistance, and thermal conductivity, making it suitable for various applications such as tooling, wear parts, and surface protection. The specific properties of the cladding layer can be adjusted by varying the composition and ratio of the tungsten carbide and metal alloy powders in the blend.
Overall, the blended powder of tungsten carbide and metal alloy powder offers a versatile and customizable solution for laser cladding applications, providing enhanced wear resistance, hardness, and other desired properties to the final cladding layer.
WC Blend,Blended Powder,High Hardness Powder,Blended Coating Powder
Luoyang Golden Egret Geotools Co., Ltd , https://www.xtcwelding.com